Building Statistics
General Building Data
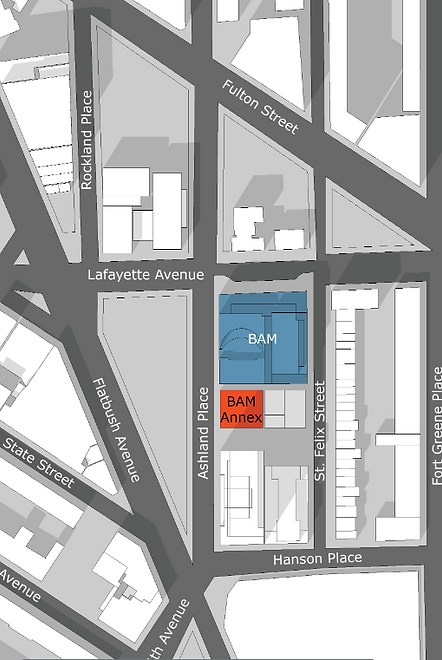
Building name | BAM Fisher
Location | 321 Ashland Pl, Brooklyn NY, 11217
Building Occupant Name | Brooklyn Academy of Music
Occupancy and Function | Group A-1 Theater
Size | 40,000 SF
Stories Above Ground | 7
Stories Below Ground | 1
Dates of Construction | 10/1/2010-5/1/2012
Construction Cost | $25.2 million
Overall Project Cost | $52 million
Project Delivery Method | Design Build with CM at Risk with a GMP
The BAM Fisher Building, also known as the BAM Annex (red), is located in Brooklyn, NY directly next to the existing BAM Peter Jay Sharp Building (blue) at 30 Lafayette Ave. Credit: H3 Architects
Architecture and Historical Significance | The Salvation Army Building was built in 1927 on the current BAM Fisher site. Although the building is not an official landmark (it acts as a infill building in a historic district), the team still wanted to celebrate the its history. Through collaboration with the Landmark's Preservation committee, H3 Architects restored the existing facade. The facade was originally closed off with no windows due to fear of crime, but the architects opened up the lobby by implementing glass doors and large sheets of fixed glass at street level in arched openings. The new construction acts as a modern take on the traditional brick cladding. The raised addition is comprised of a linear arrangement which draws the eye across.
Codes Used
State Energy Code. The New York State Energy Conservation Construction Code, current edition.
New York State Department of Health (NYSDOH): Radon requirements.
ASHRAE Handbook of Fundamentals, current edition.
ASHRAE 62.1, Ventilation for Acceptable Indoor Air Quality, current edition.
ASHRAE 52.2, Method of Testing General Ventilation Air-Cleaning Devices for Removal Efficiency by Particle Size, current edition.
ASHRAE/IESNA Standard 90.1 current edition.
SMACNA IAQ Guidelines for Occupied Buildings Under Construction
South Coast Air Quality Management District (SCAQMD) 1168, SCAQMD 1113
U.S. Energy Policy Act 1992
Zoning | C6-1 , the C6 districts are located in Manhattan, downtown Brooklyn, and downtown Jamaica and accommodate a wide range of commercial uses. C6-1 is an area outside central business cores and the buildings have a commercial floor area ratio (FAR) of 6.0.
Architecture
Building Enclosure
Building Facades | All building facades are made in a tradition brick style. The brick on the new construction quietly compliments the restored brick facade of the historical face whilst distinctively using a different aesthetic. The Fisher building seamlessly fits in with the surrounding buildings including the BAM Peter Jay Sharp Building located adjacent. The Salvation Army house existing exterior walls use batt insulation inside of a new built out gypsum board wall. The new construction exterior is a mass masonry wall using fully grouted CMU blocks. The outside face of the wall uses rigid insulation and batt insulation between the built out wall on the interior. The thickness of the wall varies from 12 to 19 inches dependent on the CMUs used. The varying thickness also comes from if there is GWB finished wall placed on top of the CMUs or if the wall is just pained out. In addition to the brick, there is an area of the new exterior wall that has a stucco finish, which is the thinnest of the wall sections.
Roofing | The lower roof atop the exiting facade consists of clay tiles. Through the construction the clay tiles were restored to ensure adequate performance.
The roof atop the new portion of the building consists of an outdoor roof garden. The roofing materials are high albedo. This means the materials have a solar reflectance index (SRI) equal to or greater to 78 for at least 75% of the roof area.
Aluminum Windows | The large windows on the third story at the dance studio are Kawneer's GLASSvent Windows. These windows meet LEED sustainable requirements for thermal performance using a thermally improved flush design with structural silicone glazed for 1/4" to 1" infills.
Steel Windows | The traditional style window treatments on the second floor are Hope's Windows Landmark175 Series steel windows. Also complying with LEED standards for glazing, these windows have a narrow sightline of 2-3/16" with a double pane system.
The BAM Fisher building achieved a LEED Gold rating, being the first theater to do so in the Manhattan area for new construction. This rating ties in to BAM's goal to create a unique arts facility that is environmentally responsibly in a growing sustainability focused society.
Through the efforts of the designers to create a sustainable space, the building achieves a 40% reduction water usage and a 22% reduction in greenhouse gas emissions. The project team also used low emitting material in all building interior finishes and according to BAM Director of Capital Projects Jonathan Jones approximately 97% of the construction waste was recycled.
Another design feature included in the BAM Fisher building is the incorporation of a rooftop terrace. The terrace not only provides a beautiful exterior space for events, the use of white high albedo roofing materials reduce the heat island effect.
Sustainability Features


Previous Salvation Army Building Credit: H3 Architects
BAM Fisher Building | Showing restoration of historic facade and new construction
Credit: Cline Bettridge Bernstein Lighting Design
Lighting System
The lighting design for this building won a Lumen Award of Merit. The lighting designers worked to create a space that was vibrant, alive, and fun. The design utilizes fluorescent, halogen, and metal halide lamps primarily throughout the spaces. Lutron zoning controls and occupancy sensors are also used in several spaces using Lutron Ecosystem through the XPS Softswitch system. Patrons are drawn to the building by the interior lighting glowing from within. Once inside the lobby, patrons are faced with a large mural that covers the majority of the adjacent wall which is lit vwith MR16s. The lobby also consists of a grand stair with color changing LED fixtures implementing DMX controlling. The cream colored ceiling creates a floating effect with LED strips hidden behind acoustical panels. The black box theater contains incandeseccnt wide-beam quartz lamp pendants that are mounted on flexible cables. This allows them to be easily moved on the mesh ceiling grill to accomate the needs of the theatrical lighting and equipment on a per performance basis. In the words of the lighting designers, "Looking out over the community that the building serves, the space is emblematic of the projectas a whole: a beautiful destination, respectfully yet imaginatively woven into the neighborhood."
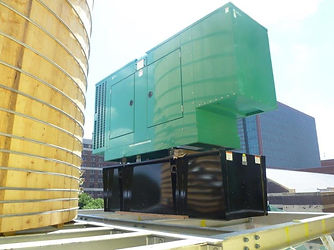
Roof Generator
Courtesy of: ICOR Consulting Engineers
Electrical System
Con Edison provides the building with 120/308V 3 phase power from an underground sidewalk trasnformer vault located on ashland avenue. The 120/208V 3 phase 3000A main distribution panel is located in the cellar, along with the 4000A main switchboard. On the second floor, a large electrical room controls the theater space. This room consists of a 500kVA transformer and a 75kVA transformer (for AV system) which converts 208V delta to 208/120V WYE for use with theatrical equipment. The room also has 2 DMX control panelboards (typical for theatrical lighting control) and a 1600A Dimmer panel. The fifth floor is home to the IT rack sever room which houses 12 severs. (it5-9). The rooftop emergency diesel fuelgenerator is 150kW and is connected to life safety loads, fire pump, and elevator.
Mechanical System
The BAM Fisher building has 3 Air handling units that provide a total of 25K CFM to the theater, dance studio, and back of house spaces. The units are located on the 5th and 6th floor in the main mechanical spaces. In addition, the building has 2 rooftop units that service the lobbies and vestibules along with an emergency generator. The systems are mainly variable air volume but several spaces are controlled using constant air. The air is cooled through three air cooled chillers also in the mechanical space. In the blackbox theater, flex ducts are used to allow for maximum flexibility with theatrical lighting equipment and stage scenery. Typical with many NYC buildings, there is also a water tank on the roof that is used for everyday water supply and fire supply.
Structural System
The structural system for this building is unique as the existing building façade and slabs were to be retained. As such, there are several construction joints to account for varying expansion and contract of materials. The new construction consists of a steel frame with concrete slabs on metal deck. All steel columns are wide flange. Due to the subway lines running adjacent to the property, standard slab-on-deck construction could not be used. Instead a 12in cast-in-place slab was used which allowed for less steel framing and longer spans. The building also has a new reinforced concrete foundation wall built at the back of the structure. The lobby height in the existing building was reconfigured to be two stories high. As such, additional structural support was needed. New columns were added adjacent to exiting columns and forked out into an inverted "V" at the cellar level and land on a new mat slab to avoid existing spread footings. The Blackbox Theater uses narrow braced frames that flank the theater and are connected by a full-story truss above. As the theatre is 3 stories high, the system transfers the gravity loads over the theater and increases the stiffness and reduced overturning loads at the foundation. The theater also has a hanging tension grid several stories above the stage that is capable of holding lighting equipment, scenery fly aways, and humans for servicing. The building also has a large dance studio that is double height. The space implements a "box-in-box" design theory which requires a separation of floor slab, walls, and ceiling from the remainder of the building structure to reduce vibrations from the performance space.
Construction
Fire Protection
Security
The delivery method of this building was Design Build with CM at Risk with a GMP. The building was designed by H3 architects and the construction manager was E.W Howell. All construction complies with codes and requirements set forth by city zoning and national/international codes. The overall project cost was $52 million and the building obtained LEED Gold.
The building has a 50HP fire pump connected to the main switchboard and the emergency generator. The building also has a sprinkler system thorughout. Emergency lighting and life safety loads are connected to the generator and comply with all necessary codes for group A-1 occupancies.The building has an automatic addressable fire alarm system which includes area smoke detectors, speakers and strobes.
The security system in the building consists of an access control system, alarm point monitoring, communication system, and video surveillance. The access control system is card readers and electromagnetic locks. The alarm point monitoring is duress buttons, motion detectors, leak/damage protectors and tamper switches. The communication system involves video intercom stations and is powered over Ethernet. Video Surveillance includes cameras and monitors.
Transportation
The building has one 50HP elevator. The elevator serves all floors and is large enouigh to be used for theatrical freight. The elevator is also connected to the emergency generator as required by code for high-rise buildings.
Telecommunications & Data
The telecommunication line comes from the Peter Jay Sharp Opera House, another BAM facility located adjacent to the Fisher Building. The conduit run is approximately 300’ from the existing computer room in the Sharp Opera House to where it enters the Fisher Building. The Fisher Building has 3 wall mounted cabinets for telecommunications located on the cellar, 2nd, and 6th floors.
Lighting Control
General lighting in common space is controlled by a Lutron XP Softswitch system which works using lighting zones and scene control. The lobby, rooftop terrace, stairwells, and corridors are all on this system. The XP panels are located in the mechanical room on the 6th floor.The theatrical lighting is all DMX controlled and it served by the TLG-2 panel board, TRP-1 relay panel, and 4 dimming panels located dimming room on the second floor.